Automatisierte Lagersysteme und Bereitstellungsysteme (ASRS) sind eine vielfältige Antwort auf spezifische Anforderungen des Lagerbetriebs. Jeder Lagerleiter, der mit dem Mangel an ausreichend großer Lagerfläche und Zeit für die Verwaltung der gelagerten Waren konfrontiert ist, sollte sich nicht fragen, ob er ein ASRS-System kaufen soll, sondern mit welcher Art von System er das Lager ausstatten soll.
Welche Arten von automatischen Regalbediengeräten es gibt und für welche Aufgaben sie am besten geeignet sind, erfahren Sie im folgenden Artikel. ASRS (Automated Storage and Retrieval Systems) sind automatisierte Lagersysteme und Bereitstellungsysteme in einem. Unter dem Strich, sie verbessern die Handhabung, Lagerung und Kommissionierung von Elementen in einem Lagerhaus.
Automatisierte Lagersysteme und Bereitstellungsysteme (ASRS) maximieren vor allem die Lagerdichte durch intelligentes Raummanagement – vertikal und horizontal. ASRS kooperiert mit einem Lagerleitsystem (WCS). Dadurch optimieren sie die Produktlagerung, Kommissionierungsstrategien und die Lagereffizienz. Die Wahl des richtigen ASRS-Systems trägt zu einem schnellen Return on Investment bei.
Allgemeine Aufteilung der ASRS-Systeme
Die rasante Entwicklung des E-Commerce hat dazu geführt, dass zahlreiche Automatisierte Lagersysteme und Bereitstellungsysteme (ASRS) auf dem Markt erscheinen, die mit unterschiedlichen Geschwindigkeiten arbeiten und unterschiedliche Größen und Arten nicht palettierter Waren handhaben können. Die Wahl der ASRS-Technologie hängt von den Besonderheiten Ihres Unternehmens, der Speicherdichte, den Effizienzzielen und dem Budget ab. Abhängig davon, wie Waren geliefert werden, können ASRS-Technologien grob in drei Hauptkategorien unterteilt werden:
– Kommissionierung aus Regalen,
– Picking aus Containern,
– Kommissionierung mit Robotern.
Automatisierte Lagersysteme und Bereitstellungsysteme (ASRS) – 6 wichtigste Typen
1) Karussellgestelle – Behälter werden auf horizontalen oder vertikalen Karussellgestellen platziert mit Waren. Durch das verschiebbare Regalsystem gelangt die Ware direkt zum Entnahmemitarbeiter, ohne den Bahnhof verlassen zu müssen. Diese Art von Racks gilt als zuverlässig und kostengünstig. Allerdings sind sie nicht sehr effizient. Sie erlauben jeweils nur die Lieferung eines Regals.
2) Lagerlifte (VLM – vertikales Hebemodul) – sparen Lagerraum. Die Tabletts sind vertikal in einem System angeordnet, das einem Aufzug ähnelt. Das System klappt aus einem zentral positionierten Beschicker mit beidseitig geschlossener Bodenkolonne. Besonders nützlich sind Regale dieser Art in Lagerhallen, in denen Waren ungewöhnlicher Größe gelagert werden. Wie bei Karussell-ASRS-Systemen besteht ihr Hauptnachteil darin, dass sie eine geringe Kapazität und Ineffizienz haben.
3) Miniload-System – funktioniert gut beim Lagern und Auslagern voller Einheiten, die normalerweise über Förderbänder an die Arbeitsplätze geliefert werden. Allerdings gilt es als unzuverlässig, da die Technologie selbst sehr alt und im Vergleich zu neueren Systemen recht langsam ist. Darüber hinaus hängt der Erfolg des Einsatzes von einem Regalbediengerät ab. Infolgedessen, fällt es aus, drohen im Lager enorme Störungen.
4) Shuttle-System – nutzt Roboterwagen (Shuttles), die sich unabhängig voneinander auf verschiedenen Ebenen bewegen, um Waren schnell zu kommissionieren und an den Arbeitsplatz zu liefern. Wagen liefern Träger (z. B. Container) an den Aufzug, der sie zu den Förderbändern und von dort zu den Arbeitsplätzen transportiert. Der Nachteil dieses Systems ist sein hoher mechanischer Aufwand. Ein Ausfall des Aufzugs in einem Gang kann auch den Zugang zu allen Waren im Gang blockieren. Der Vorteil besteht darin, dass Roboterwagen sehr schnell sind und die Produkte sofort an den Mitarbeiter liefern.
5) Roboter-Würfel-basiertes ASRS – hat eine charakteristische Struktur – dicht angeordnete Behälter, die einen Würfel bilden. Zu dieser Art von Systemen gehört beispielsweise AutoStore. Intelligente Roboter bewegen sich selbstständig auf einem der Struktur überlagerten Raster. Sie mischen, sortieren, holen die Behälter zurück und bringen sie zum Arbeitsplatz, damit ein Mitarbeiter die Bestellung abschließen kann. Die Roboter sind drahtlos mit dem System verbunden und werden aufgeladen, wenn sie nicht verwendet werden. Alles wird vom Controller und der integrierten Software überwacht. Alles wird vom Controller und der integrierten Software überwacht. Das System bietet ein Höchstmaß an Lagerdichte und ist somit eine ideale Lösung bei begrenztem Lagerraum. Dank seines modularen Aufbaus lässt es sich problemlos an Ihre sich ändernden Anforderungen anpassen. Anders ausgedrückt, AutoStore ist die einzige Technologie, die den vollständigen Kommissionierungs- und Verpackungsprozess ermöglicht.
6) Fahrerlose Transportfahrzeuge – technisch gesehen können sie nicht als reine Automatisierte Lagersysteme und Bereitstellungsysteme (ASRS) bezeichnet werden, sind aber eine gute Lösung für die Optimierung des Lagerbetriebs. Sie garantieren eine automatisierte Umlagerung. Eine Flotte mobiler Roboter entnimmt Artikel aus Lagerregalen und transportiert sie zum Bediener oder übergibt Kommissionierbehälter an feste Regale. Roboter können vom Typ AGV oder AMR sein. Allerdings verfügen fahrerlose Transportfahrzeuge nur über begrenzte Ladungsmöglichkeiten. Kurz gesagt, verglichen mit anderen Lagerlösungen benötigen sie auch recht viel Platz.
Automatisierte Lagersysteme und Bereitstellungsysteme (ASRS) – eine Kombination aus einem Stapelkran und einer elektrischen Laufkatze
Hierbei handelt es sich um eine Lagerlösung, die Regalbediengeräte und das Pallet-Shuttle-System (Automatic Pallet Shuttle oder APS) kombiniert. Dieses Sammellagersystem ersetzt einen Gabelstapler durch Regalbediengeräte, die Lasten mithilfe eines Elektrostaplers abholen und abladen. Der Hauptunterschied zwischen der halbautomatischen und der automatischen Version des Pallet-Shuttle-Systems besteht in der Art und Weise, wie der Elektrowagen auf dem Regal positioniert wird. Im ersten Fall bewegt der Gabelstaplerfahrer das Pallet Shuttle an den Anfang des Kanals. Im zweiten Fall wird das Pallet Shuttle zwischen den Ein- und Ausgangsstationen und den einzelnen Lagerebenen und -kanälen per Regalbediengerät transportiert, ohne dass Mitarbeiter der Anlage eingeschaltet werden müssen.
ASRS mit Pallet-Shuttle-System – Vorteile
– Effizienzsteigerung – Flurförderzeuge und Elektrostapler legen ihre Wege schnell zurück,
– ununterbrochener Betrieb – das Pallet Shuttle wird auf das Regalbediengerät geladen, was seinen vollen Betrieb mit hoher Arbeitsbereitschaft gewährleistet,
– APS beschleunigt den Bestellvorbereitungsprozess oft erheblich,
– Automatisches Transportmanagement der Bestellungen,
– Ausnutzung maximaler Lagerkapazität,
– Sicherheitsgarantie.
Die Auswahl an Lagerlösungen im Markt der Intralogistik ist enorm. Eine geeignete Automatisierte Lagersysteme und Bereitstellungsysteme (ASRS) zur Installation in einem Lager erfolgt in der Regel mithilfe spezieller Berechnungstools. Kurz gesagt, das Ergebnis der Berechnung welche Lagerlösung wie viel Platz und Geld kostet, stellt Olaf Oczkos für interessierte Kunden zur Verfügung. Diese Dienstleistung gilt auch für Anbieter von Lagerlösungen.
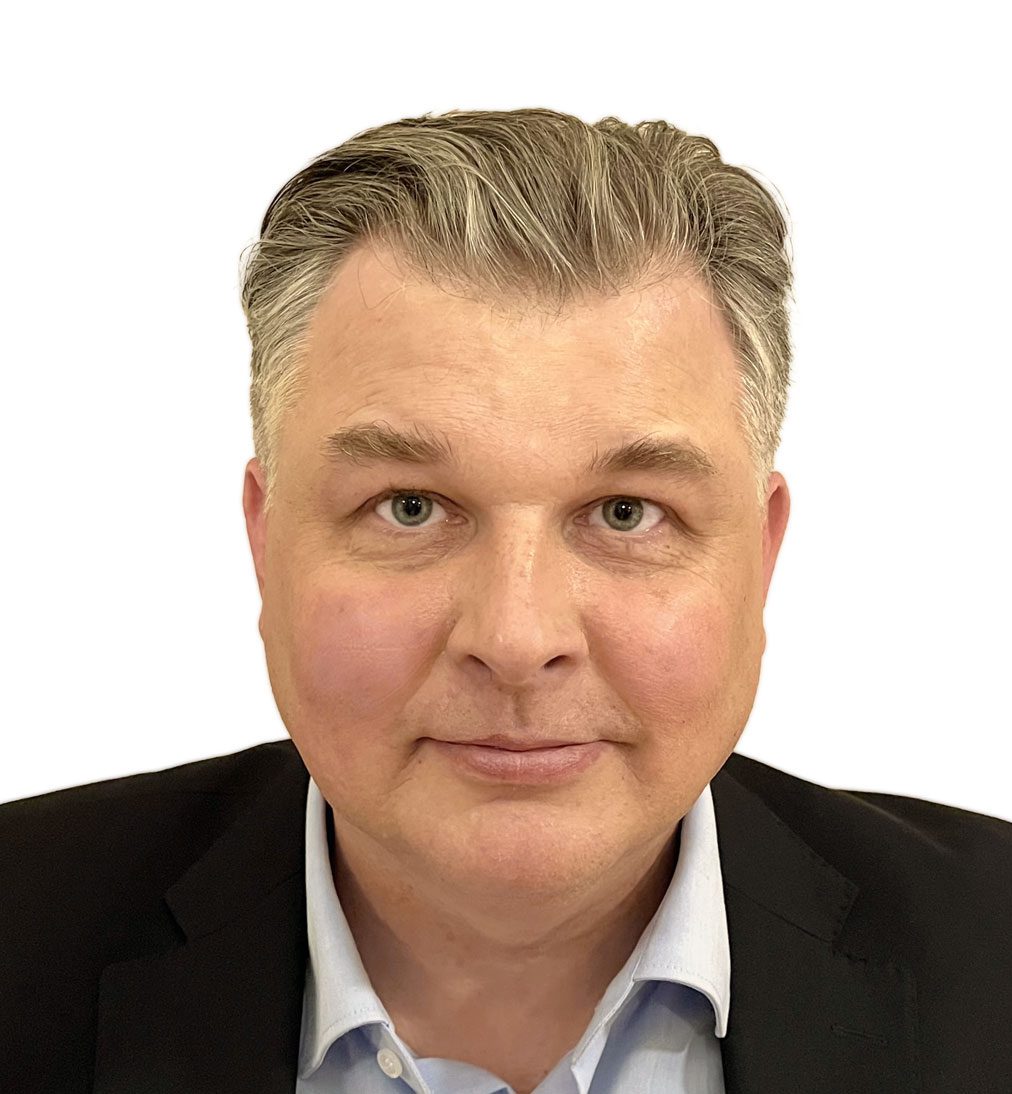
Ich bin Herausgeber von LogistikNachrichten.de , Gazetalogistyka.pl und PalettenReport.de
Zudem betreibe ich WarehouseAutomationGuide, PalettenSymposium und Petfoodindex